The Best Strategy To Use For Why Design for Manufacturing Is an Integral Part of Your
Things about Why Design for Manufacturing Is an Integral Part of Your

Business, however, are most knowledgeable about repetitive procedures like manufacturing and deal processing, where the work does not alter much and surprises are rare. Such procedures behave in an organized way as the usage of resources boosts. Include 5% more work, and it will take 5% more time to complete.
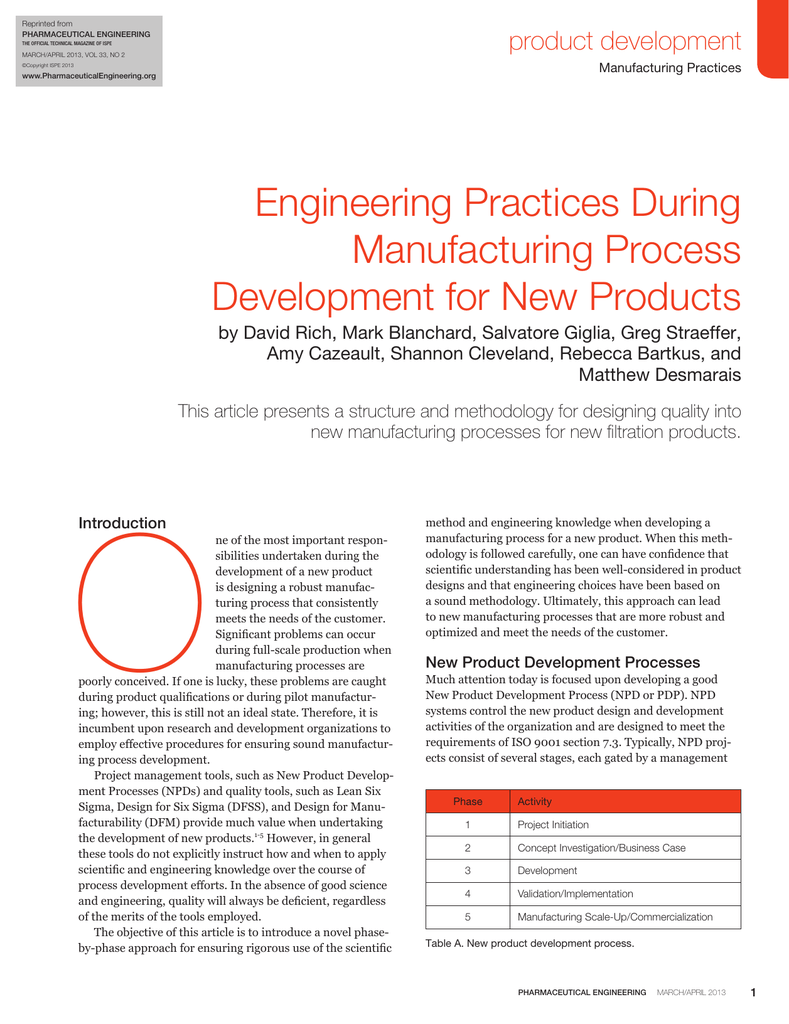
Product Development Process - Asuragen - Asuragen
As utilization boosts, hold-ups lengthen dramatically. (See the exhibit "High Usage Results In Hold-ups.") Include Found Here , and finishing it might take 100% longer. However couple of individuals understand this result. In our experience with numerous product-development teams, we have actually found that many were significantly overcommitted. To finish all jobs on time and on spending plan, some companies we dealt with would have needed at least 50% more resources than they had.
It reveals that with variable procedures, the quantity of time jobs invest on hold, waiting to be dealt with, rises steeply as usage of resources increases. Though the curve changes somewhat depending on the job work, it always turns dramatically upward as usage nears 100%. It holds true that some irregularity is the outcome of an absence of discipline, which some product-development jobs (like creating parts for an airplane model or performing clinical trials) consist of more-repetitive work.

Sustainable product development and manufacturing by considering environmental requirements - ScienceDirect
Product Development Process 101 - Smartsheet - Truths
They do not comprehend how queues affect economic efficiency. High utilization of resources undoubtedly creates queues of projects. When partially completed work sits idle, waiting for capacity to become available, the period of the total project will grow. Lines also delay feedback, causing developers to follow ineffective courses longer. They make it tough for business to adjust to progressing market needs and to discover weaknesses in their product prior to it's too late.
Even when supervisors understand that they're developing queues, they hardly ever understand the economic cost. Although that expense can be quantified, we have actually found that the vast bulk of business don't calculate it. Supervisors require to weigh line expenses against the costs of underutilized capacity in order to strike the right balance.